What is Metal Surface Treatment-Surface Finishing Process
Metal surface treatment or machining surface finish, is a process method of artificially forming a surface layer on the surface of the substrate material, which is different from the mechanical, physical, and chemical properties of the substrate. In a broad sense, Metal surface treatment includes pretreatment, electroplating, painting, chemical oxidation, thermal spraying, spraying surface, and many other physical and chemical process methods. Pretreatment includes sandblasting, polishing, mechanical grinding, cleaning, sweeping, deburring, degreasing, descaling, surface heat treatment, etc. The purpose of metal surface treatment is to meet the product’s corrosion resistance, wear resistance, decoration or other special functional requirements.
How to improve surface finish inmachining
In the process of processing, transportation, storage, etc., the surface of the workpiece is often covered with oxide scale, rust molding sand, welding slag, dust, oil, and other dirt. If the coating can be firmly attached to the workpiece, the surface of the workpiece must be cleaned before painting. Otherwise, it will affect the bonding force and corrosion resistance between the coating and the metal. Even more, it also makes the matrix metal continue to corrosion even if there is coating protection. So it will cause the coating to peel off and affect the mechanical properties and service life of the workpiece. Therefore, the metal surface treatmentof the workpiece before painting is an important guarantee and measure to obtain a high-quality protective layer and prolong the service life of the product.
In terms of technology,metal surface treatment can be classified as follows
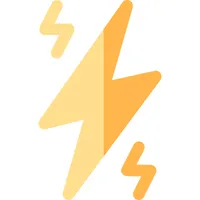
1.Electrochemical method
This method uses electrode reaction to form a coating on the surface of the workpiece.
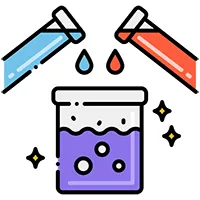
2. Chemical method
This method is no current action and uses chemical interaction to form a plating layer on the surface of the workpiece.
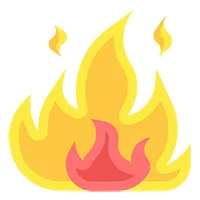
3.Hot working methods
The material is melted or thermally diffused under high-temperature conditions to form a coating on the surface of the workpiece.
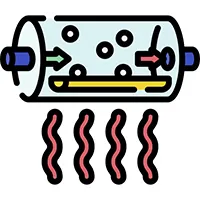
4. Vacuum method
This method is no current action and uses chemical interaction to form a plating layer on the surface of the workpiece.
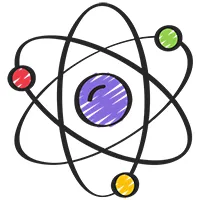
5.Other methods
There are Mainly mechanical, chemical,
electrochemical, physical methods.
All the methods of surface treatment can be subdivided as follows
Classification by technology | Subdivision | Interpretation | Surface treatment name |
Electrochemical method | Electroplate | In the electrolyte solution, the workpiece is the cathode,and the process of forming a coating on the surface under the action of external current is called electroplating. The coating may be metal, alloy,semiconductor, or containing various solid particles. | Copper plating, Nickel plating |
Oxidation | In the electrolyte solution, the workpiece is the anode, and the process of forming an oxide film on the surface under the action of external current is called anodic oxidation. | Anodizing of aluminum alloys | |
chemical method | Chemical conversion coating treatment | In the electrolyte solution, the metal workpiece is in the absence of external current action. The chemical substance in the solution interacts with the workpiece to form a coating on its surface, which is called chemical conversion coating treatment | Bluing, phosphating treatment, passivation treatment and chromate treatment of metal surface |
Electroless plating | ln the electrolyte solution, the surface of the workpiece is catalytically treated without the action of external current. Due to the reduction of chemical substances in the solution, certain substances are deposited on the surface of the workpiece to form a plating process called electroless plating. |
Electroless nickel, electroless copper plating | |
Hot working methods | Hot dip coating | The process in which a metal workpiece is placed in molten metal to form a coating on its surface is called hot dip cating. | Hot dip galvanizing, hot aluminizing plating |
Thermal spraying | The process of atomizing molten and spraying it on the surface of the workpiece to form a coating is called thermal spraying. | Thermal zinc spray, thermal spray aluminum | |
Hot stamping foil | The process of heating and pressing metal foil to cover the suface of the workpiece to form a coating layer is called hot stamping foil. | Aluminum foil hot stamping | |
Chemical heat treatment | The process of contacting and heating the workpiece with chemical substances and making a certain element enter the surface of the workpiece under high temperature is called chemical heat treatment. | Nitriding process, carburizing process | |
Overlay welding | By welding, the process of depositing molten metal on the surface of the workpiece to form a welding layer is called sufacing welding. | Wear-resistant alloy weld ovwrlay | |
Vacuum method | Physical vapor deposition(PVD) | Under vacuum conditions, the metal is vaporized into atoms or molecules or ionized into ions and directly deposited on the surface of the workpiece to form a coating. The process is called physical vapor deposition coating, and the deposition particle beam comes from non-chemical factors. | Evaporative plating, Sputtering plating, Ion plating, TIN, TiCN plating, CrN, D-AC/TiNF, TiIN, D-AICrN, D-CR/CrAIN, D-AL/AITiN, D-AS/AISiN, D-AX/AIXiN, D-AO/AIFNM, D-ACX/AICiSi,D-DLC,DH-DLC. |
lon implantation process | The process of implanting different ions into the surface of a workpiece under high voltage to modify its surface is called ion implantation. | Boron injection | |
Chemical vapor depostition CVD process | Uner low pressure ( sometimes also normal pressure), the process in which gaseous substances form solid deposition layers due to chemical reactions on the surface of the workpiece is called CVD coating. | CVD Silicon Oxide, Silicon Nitride CVD | |
Other methods | Painting | The process of applying paint (organic or inorganic) to the surface of the workpiece to form a coating by spraying or brushing is called coating. | spray paint, paint |
Strike plating | The process of forming a coating layer on the surface of the workpiece by the mechanical impact is called strike plating. | Impact galvanizing Copper strike plating Strike nickel plating |
|
Laser surface treatment | The process of irradiating the workpiece surface with a laser to change its structure is called laser surface treatment. | Laser quenching Laser remelting |
|
Ultra hard film technology | The technology of preparing a super hard film on the surface of the workpiece by a physical or chemical method is called super hard film technology. | Diamond films, Cubic boron nitride films |
|
Electrophoresis process | The workpiece is placed into the conductive water-soluble or water-emulsified paint as an electrode to form solution circuit with the other electrode in the paint. Under the action of the electric field, the coating solution has dissociated into charged resin ions, the cations move to the anode. These charged resin ions, along with adsorbed pigment particles, are electrophoresed to the surface of the workpiece to form a coating. This process is called electrophoresis. | Electrophoresis plating | |
Electrostatic spraying | Under the action of DC high voltage electric field, the atomized negatively charged paint particles are directed to fly to the positively charged workpiece to obtain the paint film. The process is called electrostaitc spray painting. | Static paint spraying |
The examples for surface finish chart
Surface treatment name | Color | Physical example |
Copper plating nickle plating |
Red bronze, Green bronze | ![]() |
Anodizing of aluminum alloys | Black, champagen, bronze, imitation steel, gold, purple gold, red, green, white, frosted oxidation. bright oxidation | ![]() |
Bluing, phosphating, passivation an d chromate treatment of metal surface | Blue black, black, natural color, color/multi color | ![]() |
Electroless nickel plating Electroless Copper |
Silver whiter to yellow, red bronze, bronze | ![]() |
Hot Galvanizing Hot aluminizing |
Silver white | ![]() |
Thermal spraying zinc Thermal sprayed aluminum |
Silver white | ![]() |
Hot stamping aluminum foil | Customized multi color | ![]() |
Nitriding carburization |
Dark gray | ![]() |
Overlay welding Wear-resistant alloy | Dark gray | ![]() |
Evaporative plating Sputtering plating, lon plating.TiN,TiCN,CrN, D-AC/TiNF, TiAIN, D-Ar/AICrN, D-CR/CrAIN, D-AL/AITiN, D-AS/AISiN, D-AX/AIXiN, D-AO/AIFN, D-ACX/AICiSi, D-DLC,DH-DLC |
multi color | ![]() |
Boron injection | ![]() |
|
Vapor Deposition of Silicon Oxide,Silicon Nitride | Black | ![]() |
spray paint,paint | Multi color | ![]() |
Impact galvanizing | ||
Laser quenching Laser remelting |
![]() |
|
Diamond film, Cubuc boron nitride film |
![]() |
|
Electrophoresis | Multi color | ![]() |
Static spraying | ![]() |