6 benefits of thread rolling
What is Thread Rolling?
Thread rolling is a cold working process that forms threads by rolling a metal blank under high pressure through a set of thread rolling dies.
Compared with other widely used threading processes such as thread cutting and thread grinding, thread rolling is no a subtractive method, but a deformative or transformative methods.There are four main types of thread rolling, including flat dies, two-die cylindrical, three-die cylindrical, and planetary dies. Flat dies are the most commonly forming method in making external threads, and they are the most important tools for processing screw and bolts in the fastener industry.
How do the flat thread rolling dies work?
The screw blank is placed on one end of the stationary die and then the reciprocating die (also known as moving die) slides over the screw blank, which causes the screw blank to roll between the two dies forming the threads. Before the reciprocating die reaches the end of its stroke the screw blank rolls off the stationary die in a finished form.
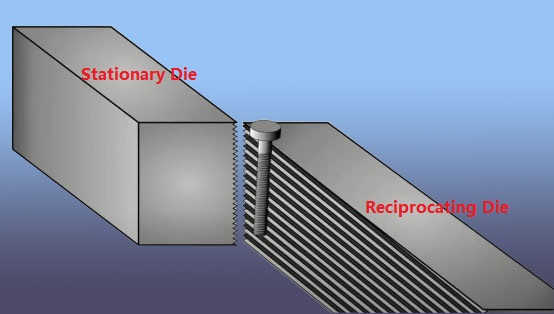
What are the benefits of thread rolling?
Thread rolling offers many benefits, including time saving, high quality, superior finish, lower costs, material strength, and so on.
1.Time Saving:
Regardless of thread depth, rolling produces the final thread in one pass through the die. The cutting and grinding process may require multiple passes to achieve full thread depth.
2.High Quality:
The thread shape geometry is stronger and more wear-resistant. It can extend the service life of parts and have better functions.
3.Superior Finish:
Rolling process produces a superior burnished finish, which is generally half that of parts with cut thread.
4.Lower Costs:
Since thread rolling does not remove material, there is minimal process waste. The process itself is much faster, tooling costs are lower, and overall material and labor costs are reduced.
5.Material Strength:
No material removed during the rolling process, which changes the physical properties of the material resulting in increasing its strength.
6.No Seam:
There is no seam at the top of the thread to increased the overall accuracy.