Abrasive Flow Machining
What is abrasive flow machining?
Abrasive flow machining (AFM), is also known as extrude honing. Because of its chamfering, deburring and polishing functions, it is also called abrasive flow deburring or fluid polishing.
AFM is an interior surface finishing process characterized by flowing an abrasive-laden fluid (such as silicon carbide or diamond power) through a workpiece.
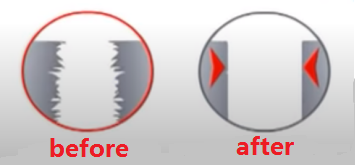
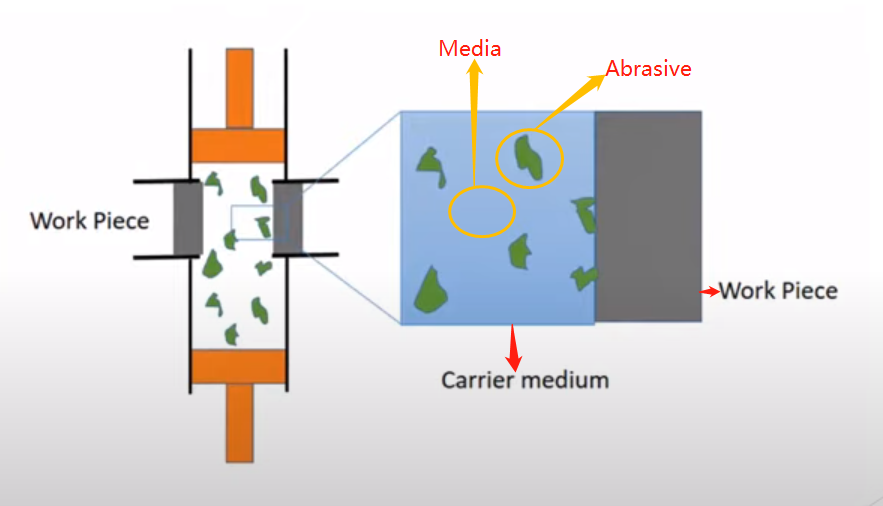
How Does Abrasive Flow Machining Work?
- There is a fixture to hold the workpiece, and a clamping system that holds all the components tightly together.
- There are two medium chambers equipped with hydraulic rams.
- AFM works by taking a chemically inactive and non-corrosive media to push it back and forth through the workpiece by hydraulic rams. Abrasive particles in the fluid contact raised features on the surface of the workpiece and remove them, where it acts as a flexible file, or slug, molding itself precisely to the shape of the workpiece.
- Rate of removal depends on the media flow rate , viscosity of the medium, abrasive particle size, abrasive concentration, particle density, particle hardness, and workpiece hardness.
What Can Abrasive Flow Machining Process?
- AFM is ideal for interior surfaces, cave convex surface, slots, intersection hole, deep cross holes, multi tiny holes, inner cross holes, cavities, fuel injector, nozzle injection valve, and other internal complex geometries that are difficult to reach with traditional grinding or polishing processes.
- AFM can machine any metal material, including titanium, super alloys, and others that have been hardened or are difficult to process. And AFM has wide rang of applications in industries such as automotive, medical, electronics, aerospace, food, precision dies and molds.
- AFM process provides high-quality results for the following surface machining:
- Radiusing or chamfering for true-edge or rounded-edge radii.
- Surface stress relief which may lead to crack propagation.
- Surface finish (Polishing) improvement with preserving the geometry.
- Geometry optimization to improve the parts characteristics.
- Deburring as a resulting of boring, drilling or cutting operations.
What are the advantages of Abrasive Flow Machining?
High Efficiency:
AFM can be used for machining multiple components simultaneously, and both roughing and finishing can be completed in a single pass.
High Precision:
AFM can polish complex internal shapes to mirror finishes.
Flexible Customization:
The abrasive media can be engineered to meet the specific application requirements.
High Repeatability:
AFM process provides process control that delivers high repeatability.
Enhanced Performance:
AFM process can improve the component’s air, gas, or liquid flow to reduce or eliminate cavitation
Versatility:
AFM is applicable for both metals and non-metals.
Who offers Abrasive Flow Machining?
Whether you are working in the automotive or aerospace or medical industry, we have the knowledge and experience to meet your requirement. Please contact U-Need for your Abrasive Flow Machining needs!
To learn more about AFM or request a free quote, contact us at +86 769 23225585 or E-mail to info@uneedpm.com. We would be love to have your business.