Centerless Grinding : A Comprehensive Guide to Machining
What is Centerless Grinding?
In the field of machining, turning has received relatively high attention. But centerless grinding is also a very important part of the machining field and is used in various industries to achieve accurate and efficient grinding operations.
This process is a process in which material is removed from the workpiece by abrasive grinding without the need for a center or chuck. Compared with the traditional process, centerless grinding uses a pair of grinding wheels to grind the workpiece, one wheel controls the grinding process, and the other wheel provides support for the workpiece.
How Does Centerless Grinding Work?
The workflow of centerless grinding is the rotation of the guide wheel and the grinding wheel. The workpiece is selected between two grinding wheels for rotary grinding, and the grinding wheel removes excess material from the workpiece through the grinding product. The guide wheel controls the rotation speed of the workpiece to ensure the grinding accuracy of the product and maintain the correct clamping of the workpiece without deviation. The gap between the centerless wheel and the guide wheel determines the removal of excess parts.
What Are the Key Components of a Centerless Grinder?
Grinding Wheel:
Removes material from the workpiece through abrasive cutting.
Regulating Wheel:
Controls the rotational speed and feed rate of the workpiece.
Centerless Grinding Work Blade:
Support and position the workpiece during grinding.
Grinding Wheel Dresser:
Shapes and dresses the grinding wheel to maintain its cutting efficiency.
Regulating Wheel Dresser:
Shapes and dresses the regulating wheel to control the workpiece feed rate.
Coolant System:
Provides coolant to cool the grinding zone and flush away grinding debris.
Control Panel:
Controls the various machine functions, including wheel speeds, feed rates, and machine movements.
What Are the Different Types of Centerless Grinding?
There are three common methods used to feed the workpieces into the grinding machine: in-feed, end-feed, and through-feed. These methods determine how the workpieces are positioned and fed relative to the grinding wheels.
Type | Principle | Description | Application |
In-feed Centerless Grinding | Place the workpiece between the grinding wheel and the guide wheel, and send the grinding wheel into the workpiece to remove the excess part of the workpiece. | The diameter of the grinding wheel is usually smaller than that of the guide wheel. It can be very strict control of the grinding process | The process can be used for precision grinding of complex shaped workpieces and precision removal of a certain amount of materials, and can also effectively grind small batch workpieces. |
End feed Centerless Grinding | The workpiece is fed axially into the grinding machine between the grinding wheel and a regulating wheel. | The grinding wheel is wider than the workpiece and can remove the material at the end of the workpiece. The guide wheel controls the speed at which the workpiece rotates. | For grinding cylindrical workpieces of uniform diameter, such as shafts or rods, it is a more efficient method of grinding long workpieces. |
Through feed Centerless | The workpiece is continuously fed through the grinding machine between the grinding wheel and the regulating wheel. | The grinding wheel removes material from the workpiece as it passes through the machine. The regulating wheel controls the speed of the workpiece rotation and the feed rate. | For grinding cylindrical workpieces with the same diameter throughout the length, such as pipes, steel pipes, bars, etc., the grinding of batch workpieces is a highly productive method. |
What Materials Can Be Used for Centerless Grinding?
This process is super flexible way of grinding that can be used on all sorts of different materials. Some of the stuff people often grind using this method includes:
- Metals:
We have metals like steel, stainless steel, aluminum, brass, copper, titanium, and various alloys. - Ceramics:
We also have ceramics such as alumina (aluminum oxide) and silicon carbide. - Plastics:
And we offer plastics like Nylon, PEEK (polyetheretherketone), and PTFE (polytetrafluoroethylene).
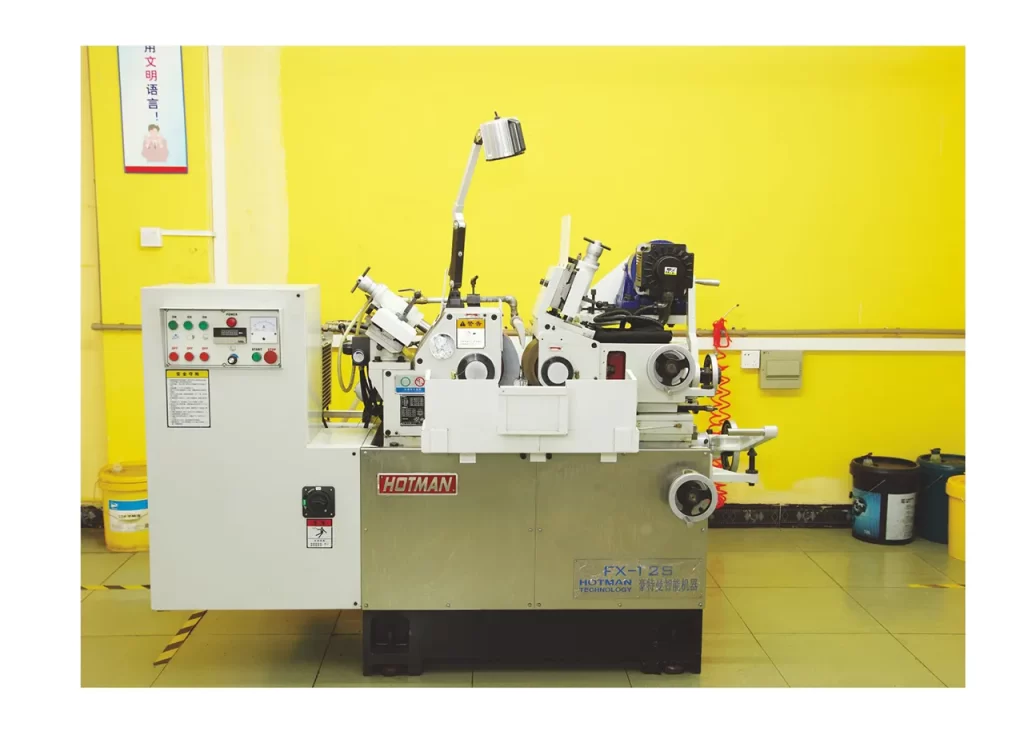
Advantages of Centerless Grinding
Disadvantages of Centerless Grinding
Summary
In this post, we have delved into the concept of centerless grinding, exploring its workings, various types, advantages and disadvantages, as well as common applications. If you would like to gain further insights on centerless grinding services, please feel free to reach out to U-NEED.