Wire EDM Services for Complex Precision Parts
The concept of wire cutting
And one method that has gained significant popularity is Wire Electrical Discharge Machining (Wire EDM).
Wire EDM, also known as EDM Wire Cutting or EDM Wire Erosion or wire-cut EDM, is a CNC machining process that utilizes a thin, electrically charged wire to cut through conductive materials with exceptional accuracy. Wire EDM services are particularly well-suited for creating complex shapes and intricate designs that would be challenging to achieve with conventional machining methods.
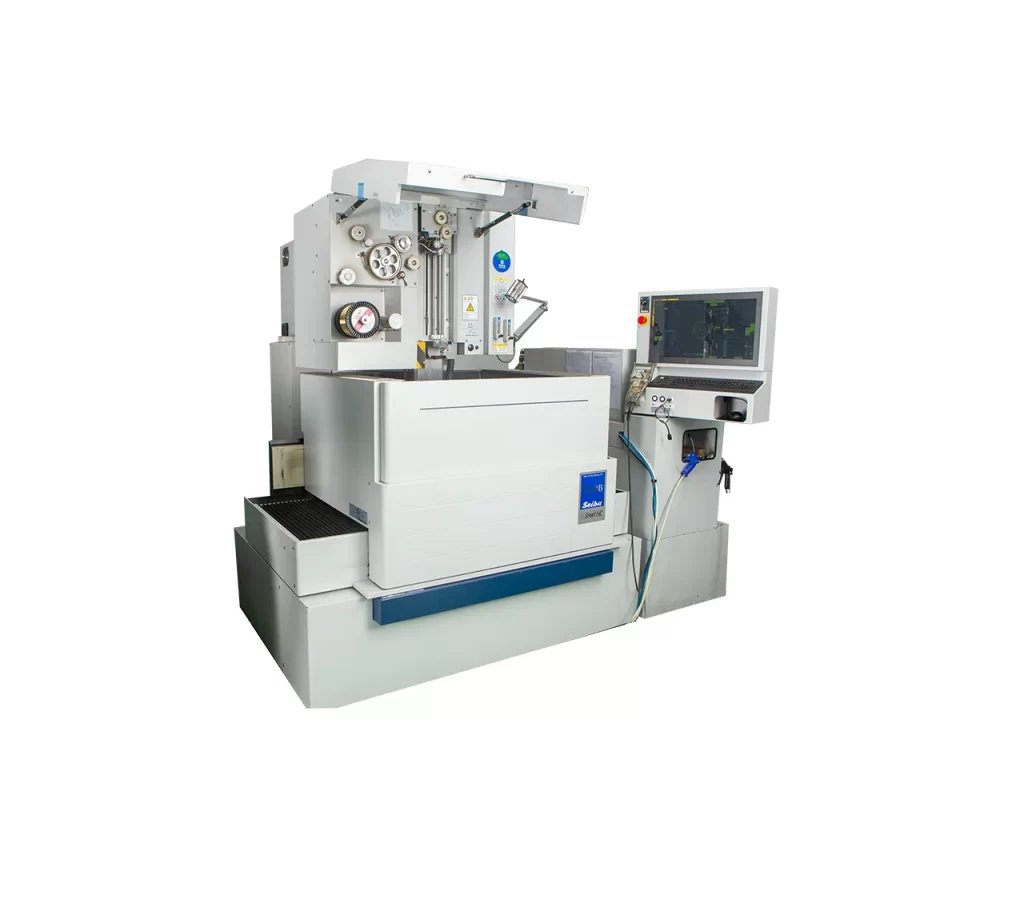
Wire EDM processing concept?
Wire EDM Services involve the controlled movement of a thin wire, typically made of brass or copper, through the workpiece while submerged in a dielectric fluid. A series of electrical discharges , or sparks, are generated between the wire and the workpiece, eroding the material and creating the desired shape. The process is highly precise and can achieve tight tolerances and excellent surface finishes.
Wire EDM two types of machining tolerances
Wire EDM is renowned for its ability to achieve tight tolerances, ensuring the precise replication of intricate part designs. Tolerances can vary based on project requirements, and two common categories are Standard Tolerance and Fine Tolerance.
Categories |
Tolerance Range |
Application Suitability |
Standard Tolerance | Standard tolerance in Wire EDM typically ranges from ±0.005 mm to ±0.010 mm (±0.0002″ to ±0.0004″). | Standard tolerance Wire EDM is widely used in industries such as automotive, aerospace, medical,and electronics, where precise and complex parts are required. Therefore, it is suitable for most applications that demand high precision but may not necessitate the utmost level of.micro-scale accuracy |
Fine Tolerance | For projects that demand even higher precision, fine tolerance Wire EDM need achieve tolerances as ±0.002 mm (±0.00008″). At U-Need, the tolerances can even achieve as tight as ±0.001mm (±0.00004″) . | Fine tolerance Wire EDM is typically utilized in specialized applications where micro-scale precision is critical. So, they are suitable for those extremely tight tolerance industries, such as microelectronics, optical devices, medical implants, and other fields. |
What are the Factors Affecting Tolerances in Wire EDM Services?
Several factors influence the achievable tolerances in Wire EDM Services, including material properties, wire diameter, cutting speed, flushing conditions, and machine capabilities. Understanding these factors and working closely with experienced professionals ensures optimal tolerances for each project.
What are the Most Suitable Materials for Wire EDM services?
Wire EDM services are compatible with a wide array of materials, including both ferrous and. non-ferrous metals Here are some examples of commonly used materials:
Type | Material | Characteristic |
Ferrous Metals | Stainless Steel | Offers excellent corrosion resistance and mechanical properties, making it ideal for various applications. |
Tool Steel | Known for its high hardness and wear resistance, making it suitable for tooling and die production. | |
Carbon Steel | Provides good strength and machinability, often used in industrial applications. | |
Alloy Steel | Combines desirable properties of different metals, offering enhanced strength and durability. | |
Non-Ferrous Metals | Titanium | Known for its exceptional strength-to-weight ratio and corrosion resistance. |
Aluminum | Lightweight and highly versatile, widely used in aerospace, automotive, and electronics industries. | |
Copper | Exhibits excellent thermal and electrical conductivity, making it ideal for electrical components. | |
Brass and Bronze | Valued for their aesthetic appeal, corrosion resistance, and low friction properties. |
What are the Key Applications of Wire EDM Services in Modern Engineering?
Wire EDM Services find extensive applications across various industries, enabling the production of complex and precision parts. Here are some key applications:
No. | Application | Description |
1 | Precision Parts Manufacturing | Wire EDM excels in manufacturing intricate components, such as gears, molds, medical implants, CNC machining aerospace parts, and microelectronics components. |
2 | Tool and Die Production | The accuracy and precision of Wire EDM make it a preferred choice for producing high-quality tooling, dies, and molds used in various manufacturing processes. |
3 | Prototype Development | Wire EDM enables the rapid production of prototypes, allowing engineers and designers to refine their designs quickly and cost-effectively. |
What are the Benefits and Limitations of the Wire EDM Services?
Here are some advantages and disadvantages of Wire EDM Services:
No. | Advantages of Wire EDM Machining | Limitations of Wire EDM Machining |
1 | Unparalleled precision and dimensional accuracy. | Limited to conductive materials. |
2 | Ability to produce complex and intricate shapes. | Slower cutting speeds compared to some other machining methods. |
3 | Excellent surface finish, reducing the need for additional post-processing. | Challenging to machine large or thick parts due to wire deflection. |
4 | Suitable for a wide range of materials, including ferrous and non-ferrous metals. | Potential for wire breakage during the process. |
5 | Cost-effective for small to medium production runs | High setup costs, high maintenance costs, and wire electrodes being particularly pricey for prolonged tasks. |
Conclusion:
Wire EDM machining is a highly precise and versatile process that enables the production of complex parts with exceptional accuracy. With its ability to achieve tight tolerances and work with a wide range of materials, Wire EDM Services have become preferred choices in various industries. By partnering with a reliable and experienced Wire EDM services provider like U-Need, you can leverage the benefits of this remarkable machining process and ensure the success of your manufacturing projects.
Let’s Start a New Project Today:
If you have a project that requires the precision and complexity that Wire EDM machining services offer, we are ready to assist you. Our team is dedicated to understanding your unique needs and providing tailored solutions to bring your ideas to life. Whether you need intricate components, tooling and dies, or rapid prototyping, we have the expertise to deliver exceptional results.
Contact us or send us E-mail (info@uneedpm.com) today to discuss your project requirements and begin a successful partnership in achieving your manufacturing goals.